無駄を一切出さず、あらゆる工程が製品の品質向上に繋がり、あらゆる資源を賢く活用する製造方法を想像してみてください。それがリーン生産方式の真髄です。企業がいかにして少ないリソースでより多くの生産を実現しているのか疑問に思ったことがあるなら、その秘密をこれから明かします。このブログ記事では、その秘密を探ります。 無駄のない製造の 5 つの基本原則、世界中の多くのビジネスを助けてきた道をたどる旅にあなたをお連れします。
目次
リーン・マニュファクチャリングとは何ですか?
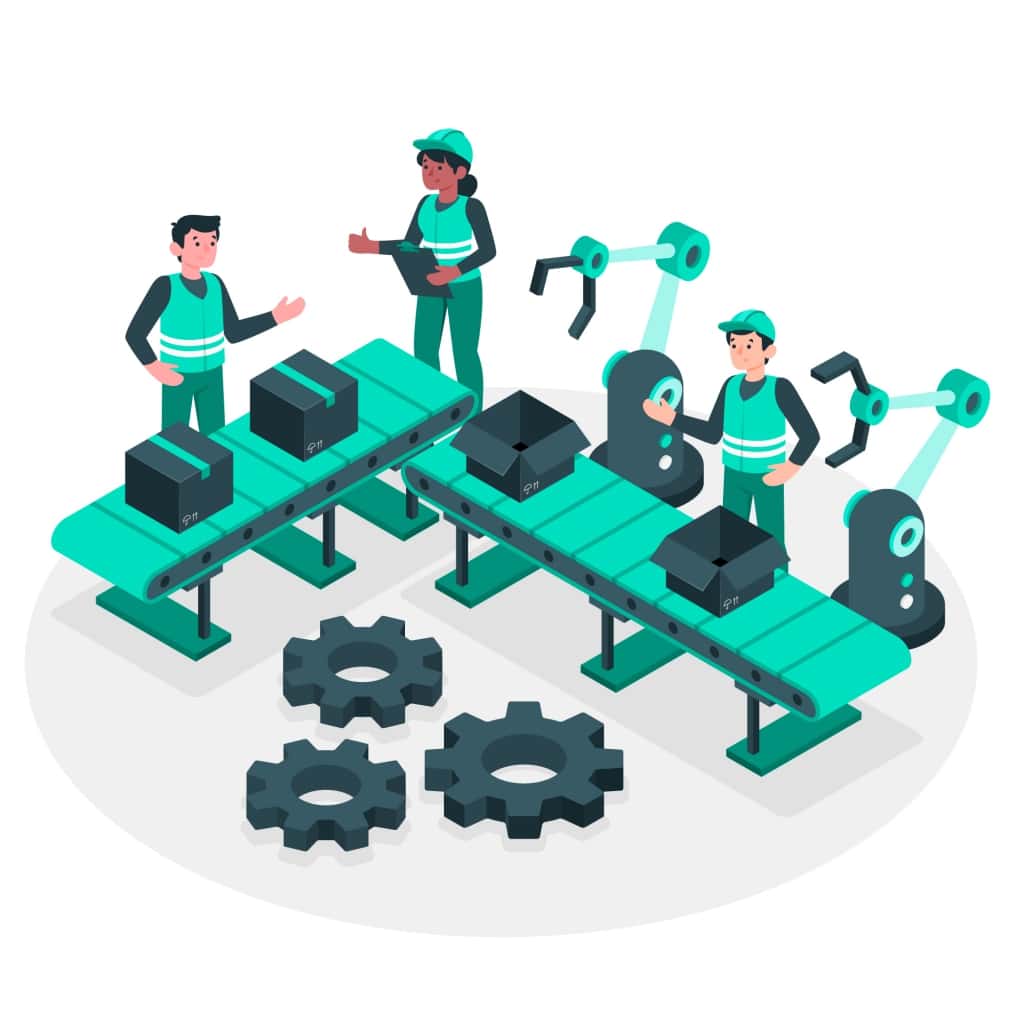
リーンマニュファクチャリングは生産に対する体系的なアプローチであり、無駄を削減し、効率を高め、顧客に価値を提供することを目的としています。 このアプローチは、 トヨタ生産方式(TPS) 現在では世界中のさまざまな業界や企業で採用されています。
リーン生産方式の主な目的は、最終的な製品やサービスに直接貢献しない不要な活動、材料、リソースを特定して削減することで、生産プロセスを簡素化することです。これにより、プロセスが合理化され、効率が向上します。
無駄のない製造の利点
リーン・マニュファクチャリングは、業務の改善を目指す企業にいくつかのメリットをもたらします。 主な利点は次の XNUMX つです。
- コスト削減:無駄のない製造では、プロセス内の無駄を特定して排除し、それによって運用コストを削減します。 これには、在庫コストの削減、エネルギー消費の削減、再作業の削減などが含まれ、最終的には企業の利益が増加します。
- 効率の向上: プロセスを合理化し、ボトルネックを解消し、ワークフローを最適化することで、無駄のない製造により業務効率が向上します。 これは、企業が同じ量またはより少ないリソースでより多くの生産を行い、投資を最大限に活用できることを意味します。
- 品質の向上: 無駄のない製造では、欠陥の根本原因を特定して解決することに重点を置き、製品品質の向上につながります。 これは、エラーややり直しが減り、顧客満足度が向上することを意味します。
- より速い配達: 無駄のない実践は、リードタイムの短縮と顧客のニーズへの迅速な対応につながります。 製品を予定通りに生産および納品できることは、企業が競争上の優位性を獲得し、顧客の期待に応えるのに役立ちます。
- 従業員のエンゲージメントを高める: 無駄のない原則は、従業員のエンゲージメント、問題解決、権限付与を促進します。 熱心な従業員はモチベーションが高まり、より前向きな職場環境と継続的な改善につながります。
無駄のない製造の 5 つの原則
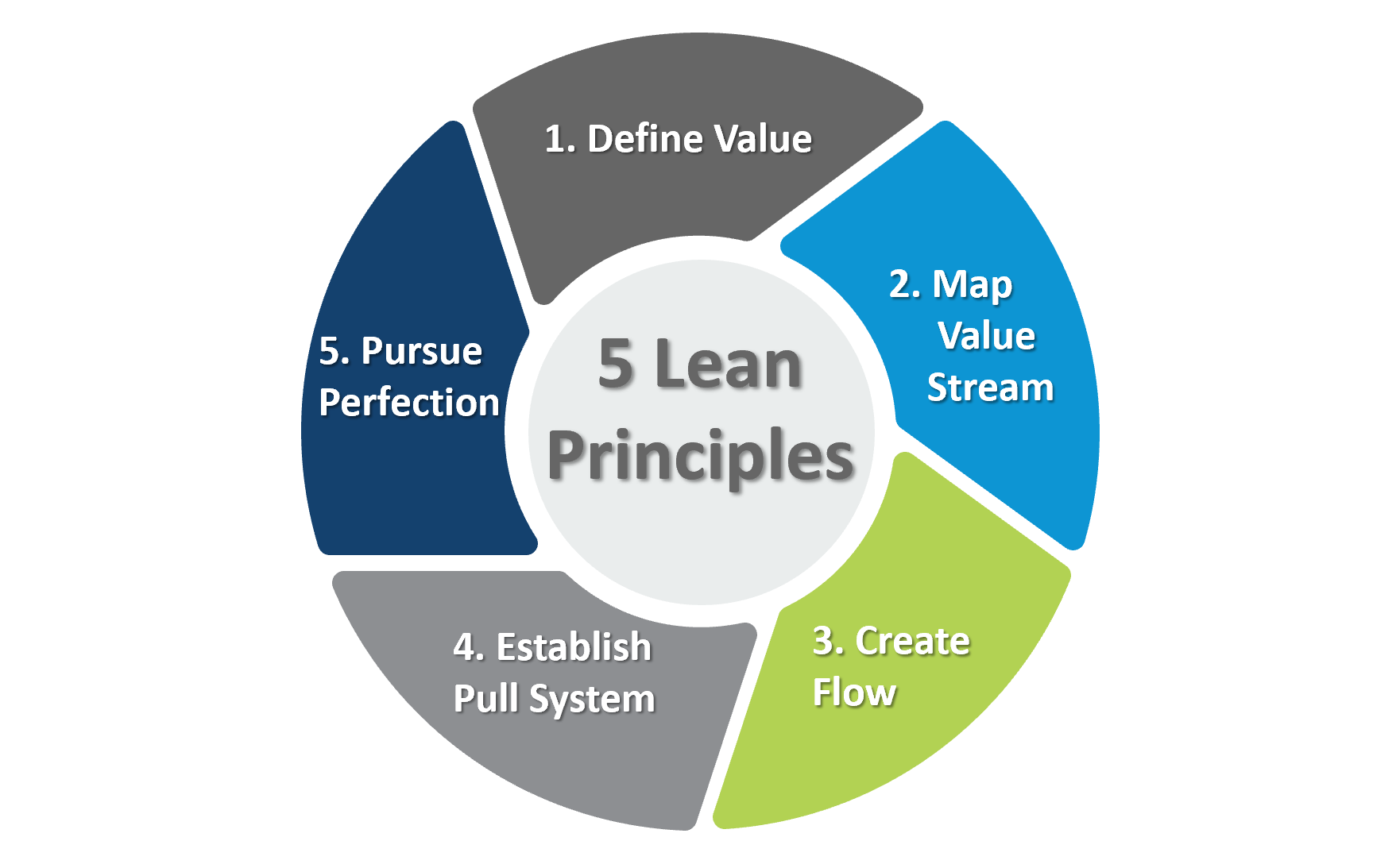
リーン生産の 5 つの原則とは何ですか? 無駄のない製造の XNUMX つの主要原則は次のとおりです。
1/ 価値: 顧客にとって重要なものを提供する
リーン生産方式の第一原則は、「価値」を理解し、提供することです。この概念は、顧客が製品やサービスにおいて真に何を重視しているかを明確に特定することに重点が置かれています。リーン生産方式における価値の捉え方は顧客中心主義であり、顧客が喜んで支払う具体的な機能、品質、または属性を特定します。これらの価値ある要素に貢献しないものはすべて無駄とみなされます。
「価値」を実現するには、企業の活動を顧客の期待とニーズと密接に一致させる必要があります。顧客が真に求めているものを理解することで、組織はリソースと労力を、付加価値をもたらすものの提供に正確に集中させ、付加価値をもたらさない要素を最小限に抑えるか、排除することができます。このアプローチは、リソースの効率的な配分を確保し、リーン生産方式の重要な側面です。
2/ バリュー ストリーム マッピング: 作業の流れを可視化する
2 番目の Lean 原則である「バリュー ストリーム マッピング」は、組織がプロセス内の無駄を特定して排除する上で重要な役割を果たします。
バリュー ストリーム マッピングには、原材料の産地から提供される最終製品やサービスに至るまで、プロセス全体の包括的な視覚的表現の作成が含まれます。 この視覚化は、プロセスに含まれる一連のアクティビティを理解するのに役立ちます。
バリューストリームマッピングは、製品やサービスに価値をもたらす活動とそうでない活動を区別するための重要なツールです。付加価値を生まない活動、いわゆる「ムダ」には、過剰生産、過剰在庫、待ち時間、不要な処理など、様々な形の無駄が含まれます。
これらの無駄の原因を特定して排除することで、組織はプロセスを合理化し、リードタイムを短縮し、全体的な業務効率を向上させることができます。
バリュー ストリーム マッピングの例を次に示します。これは、バリュー ストリーム マッピングをより深く理解するのに役立ちます。
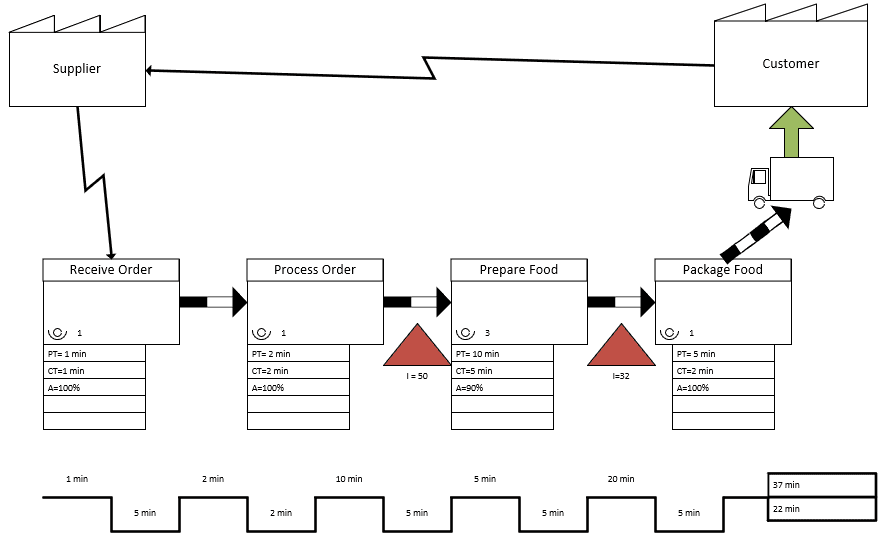
3/ フロー: シームレスな進行を保証する
「フロー」とは、組織内にスムーズで継続的な仕事の流れを生み出すことを目的としています。 フローの概念は、作業が中断または中断されることなく XNUMX つの段階から次の段階に移行し、最終的に効率を促進する必要があることを強調しています。
組織の観点から見ると、リーンはタスクや活動が妨げられたり遅れたりすることなく作業が進められる職場環境を確立することを奨励します。
「流れ」を実現する例として、製造組立ラインを考えてみましょう。 各ステーションは特定のタスクを実行し、製品は中断されることなく、あるステーションから別のステーションにシームレスに移動します。 これは、リーンにおけるフローの概念を示しています。
4/ プルシステム: 需要への対応
プル システムとは、顧客の注文に応じてサービスを作成または提供することです。 プルシステムを採用している組織は、将来の需要を想定して製品を製造することはありません。 代わりに、実際に受け取った注文に応答します。 この実践により、過剰生産が最小限に抑えられます。 XNUMXつの主要な廃棄物 リーン製造において。
- プル システムの例はスーパーマーケットです。 顧客は必要な商品を棚から取り出し、スーパーマーケットは必要に応じて棚に補充します。 このシステムにより、顧客の需要を満たす十分な在庫が常に確保され、過剰生産も発生しません。
- プル システムの別の例は、自動車ディーラーです。 顧客は興味のある車を駐車場から引き出し、試乗します。 ディーラーは、顧客の需要を満たすために必要な場合にのみメーカーに新車を発注します。
5/ 継続的改善(カイゼン)
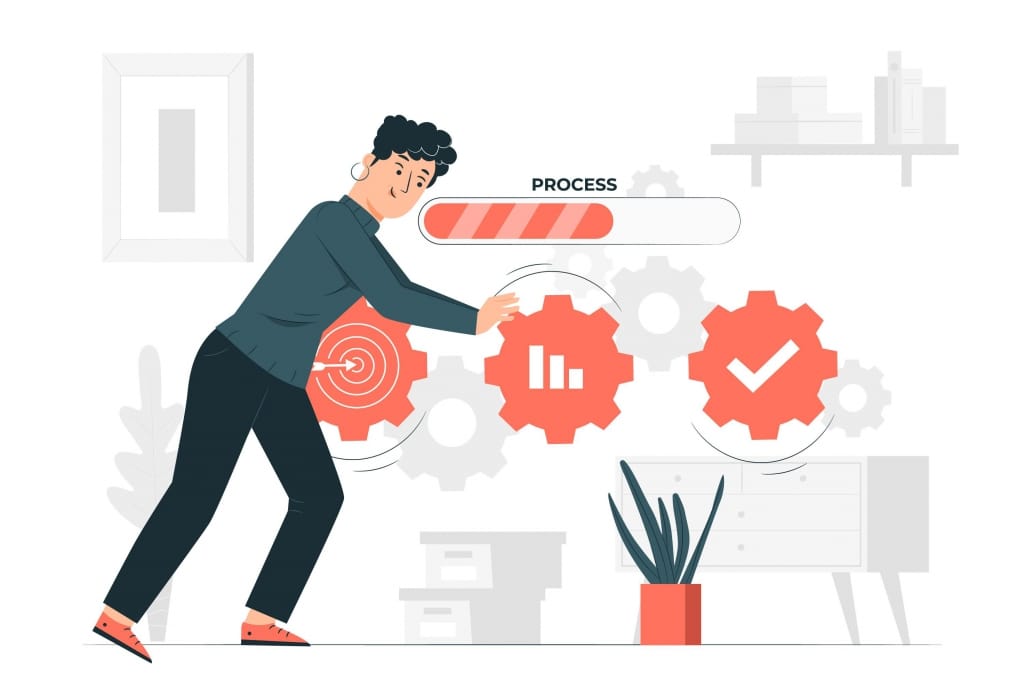
5番目で最後のリーン原則は「継続的改善」、通称「カイゼン」です。 カイゼン継続的改善プロセス。 それは、継続的な改善の文化を育むことです。
これには、急進的または抜本的な変更を加えるのではなく、時間をかけて小さな一貫した改善を行うことが含まれます。 これらの小さな改善が積み重なり、プロセス、品質、全体的な効率の大幅な向上につながります。
カイゼンの重要な側面の XNUMX つは、その包括的な性質です。 組織のあらゆるレベルからの参加を奨励し、従業員がアイデア、観察、洞察を投稿できるようにします。 このアプローチは、問題解決能力を高めるだけでなく、従業員の士気とエンゲージメントも高めます。
カイゼンは、組織がより良く、より効率的に、より効果的になろうとする継続的な動機を確実にします。 これは継続的な改善への取り組みであり、リーン文化の基本的な側面です。
最終的な考え
リーン製造業の 5 つの原則: 価値、バリュー ストリーム マッピング、フロー、プル システム、継続的改善 (カイゼン) は、組織に運用の卓越性を達成するための強力なフレームワークを提供します。
リーン製造の L5 原則を採用する組織は、効率を向上させるだけでなく、無駄を削減し、製品とサービスの品質を向上させます。
リーン・マニュファクチャリングの原則に関するよくある質問
無駄のない製造の 5 つの原則とは何ですか?
リーン製造の 5 つの原則は、価値、バリュー ストリーム マッピング、フロー、プル システム、継続的改善 (カイゼン) です。
リーン原則は 5 つまたは 7 つありますか?
さまざまな解釈がありますが、最も広く認識されているリーン原則は上記の 5 つです。
無駄のない生産の 10 のルールとは何ですか?
リーン生産方式の10原則は、一般的にリーン製造業における標準規格ではありません。リーンの原則は、前述の5つの中核原則に基づいています。一部の情報源では「ルール」として挙げられている場合もありますが、必ずしも普遍的に認められているわけではありません。