아무것도 낭비하지 않고, 모든 단계가 더 나은 제품을 만들며, 모든 자원을 현명하게 사용하는 제조 방식을 상상해 보세요. 이것이 바로 린 제조의 핵심입니다. 어떤 회사들이 어떻게 더 적은 자원으로 더 많은 제품을 생산하는지 궁금했던 적이 있다면, 이제 그 비밀을 알게 되실 겁니다. 이 블로그 게시물에서 그 비밀을 알아보겠습니다. 린 제조의 5가지 핵심 원칙, 전 세계의 많은 기업에 도움이 된 길을 안내합니다.
차례
린 생산이란 무엇입니까?
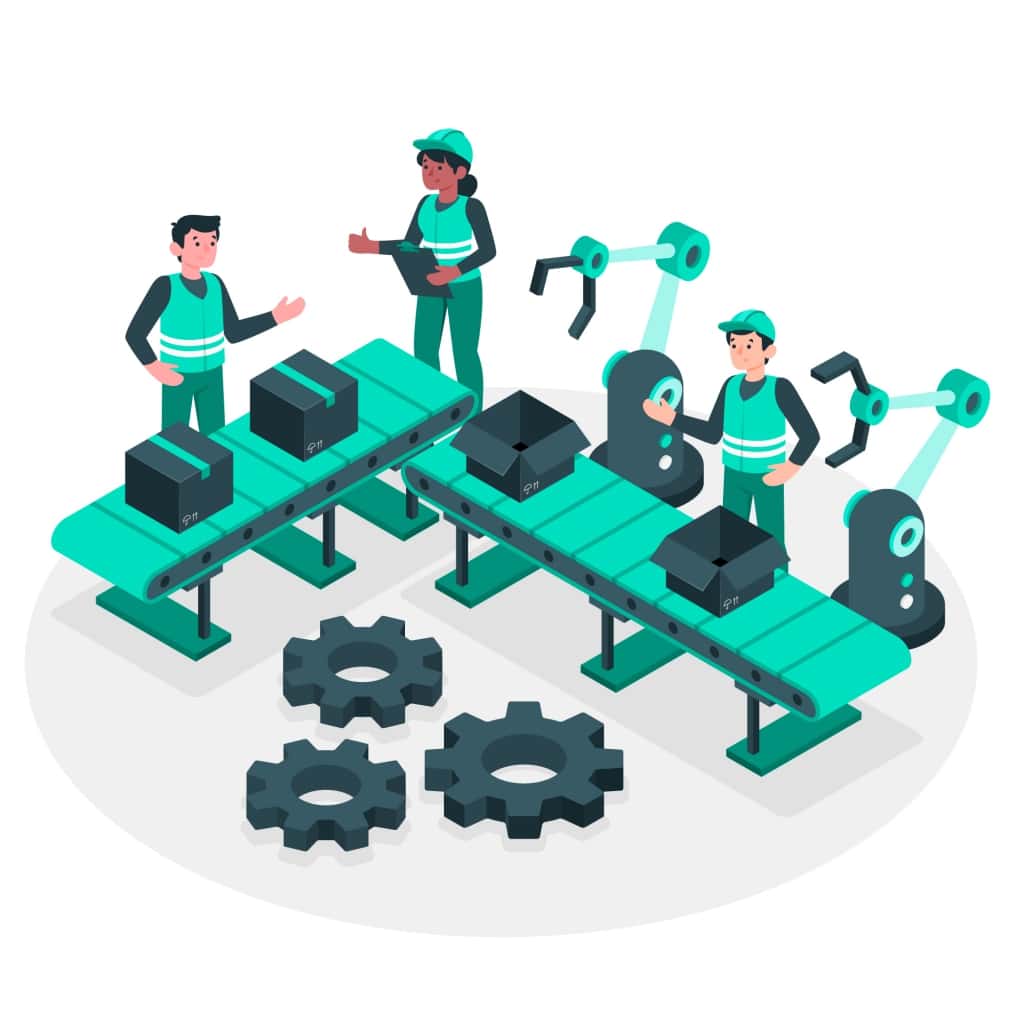
린 제조(Lean Manufacturing)는 폐기물을 줄이고 효율성을 높이며 고객에게 가치를 제공하는 것을 목표로 하는 체계적인 생산 접근 방식입니다. 이 접근 방식은 다음에서 시작되었습니다. 도요타 생산 시스템(TPS) 현재 전 세계적으로 다양한 산업과 기업에서 채택되고 있습니다.
린 제조의 주요 목표는 최종 제품이나 서비스에 직접적으로 기여하지 않는 불필요한 활동, 자재 또는 자원을 파악하고 제거하여 생산 프로세스를 간소화하는 것입니다. 이를 통해 프로세스를 간소화하고 효율성을 높일 수 있습니다.
린 제조의 이점
린 제조는 운영 개선을 목표로 하는 기업에 여러 가지 이점을 제공합니다. 다섯 가지 주요 이점은 다음과 같습니다.
- 비용 절감: 린(Lean) 제조는 공정에서 낭비되는 부분을 식별하고 제거하여 운영 비용을 절감합니다. 여기에는 재고 비용 절감, 에너지 소비 감소, 재작업 감소가 포함되어 궁극적으로 회사 수익이 증가합니다.
- 효율성 증대: 프로세스를 간소화하고 병목 현상을 제거하며 작업 흐름을 최적화함으로써 린 제조 방식은 운영 효율성을 높입니다. 이는 기업이 동일한 양 또는 더 적은 양의 자원으로 더 많은 것을 생산하여 투자 효과를 극대화할 수 있음을 의미합니다.
- 향상된 품질: 린 제조는 결함의 근본 원인을 식별하고 해결하는 데 중점을 두어 제품 품질을 향상시킵니다. 이는 오류 감소, 재작업 감소, 고객 만족도 향상을 의미합니다.
- 더 빠른 배송: 린 방식을 통해 리드 타임이 단축되고 고객 요구 사항에 더 빠르게 대응할 수 있습니다. 제품을 적시에 생산하고 배송할 수 있는 능력은 기업이 경쟁 우위를 확보하고 고객 기대를 충족하는 데 도움이 될 수 있습니다.
- 직원 참여도 향상: 린(Lean) 원칙은 직원의 참여, 문제 해결 및 권한 부여를 장려합니다. 몰입도가 높은 직원은 더욱 동기 부여가 되어 더욱 긍정적인 업무 환경과 지속적인 개선을 이끌어냅니다.
린 제조의 5가지 원칙
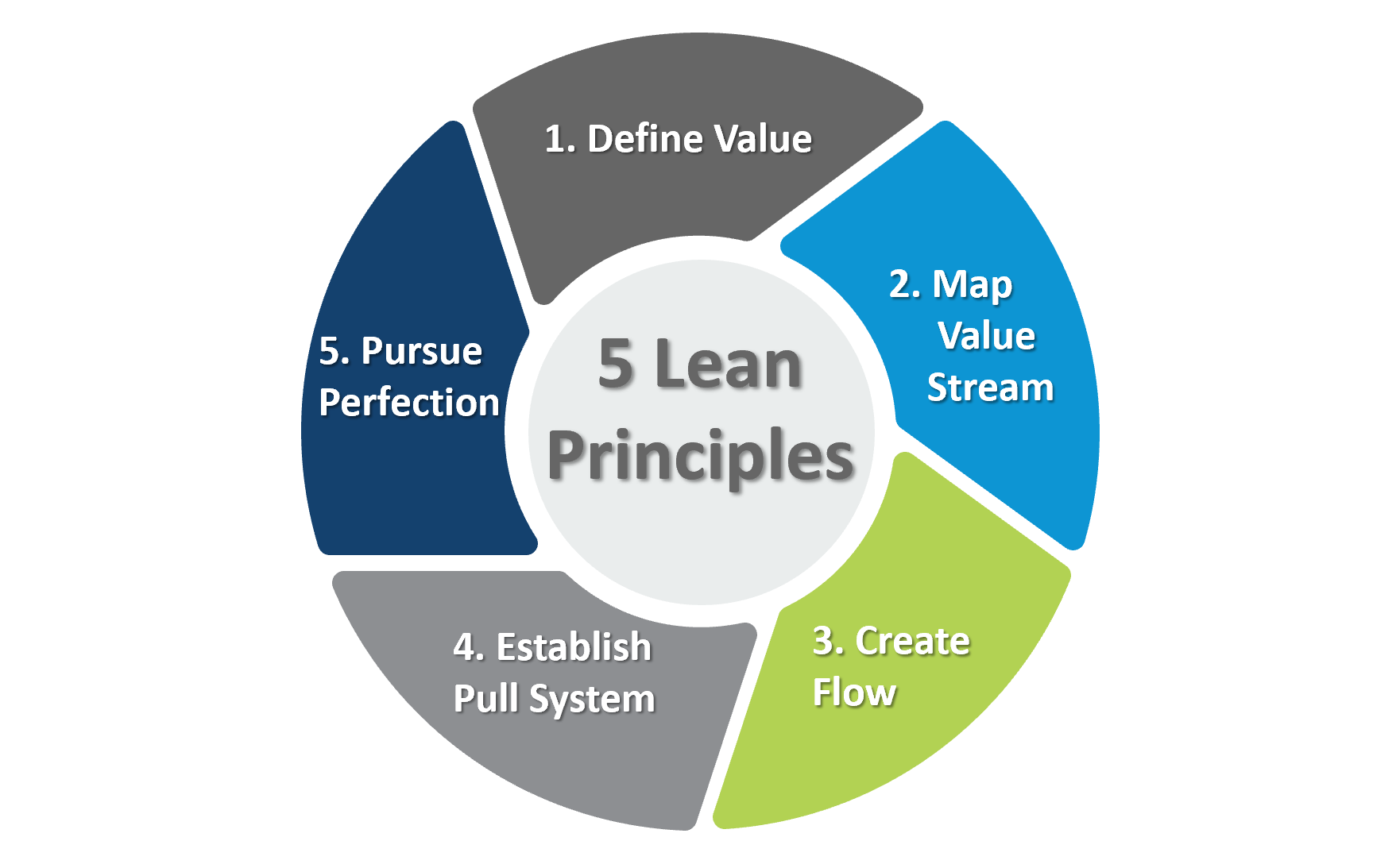
린 제조의 5가지 원칙은 무엇입니까? 린 제조의 XNUMX가지 주요 원칙은 다음과 같습니다.
1/ 가치: 고객에게 중요한 것을 제공
린 제조의 첫 번째 원칙은 "가치"를 이해하고 제공하는 것입니다. 이 개념은 고객이 제품이나 서비스에서 진정으로 중요하게 여기는 것이 무엇인지 명확하게 파악하는 것을 중심으로 합니다. 린 제조의 가치관은 고객 중심적이며, 고객이 기꺼이 지불할 의향이 있는 특정 기능, 품질 또는 속성을 파악합니다. 이러한 가치 있는 요소에 기여하지 않는 것은 모두 낭비로 간주됩니다.
"가치"를 실현하려면 기업 활동을 고객의 기대와 니즈에 맞춰 긴밀하게 조정해야 합니다. 고객이 진정으로 원하는 것이 무엇인지 이해함으로써 기업은 가치를 창출하는 요소를 정확하게 제공하는 데 자원과 노력을 집중하는 동시에 가치를 창출하지 못하는 요소는 최소화하거나 제거할 수 있습니다. 이러한 접근 방식은 자원의 효율적인 배분을 보장하며, 이는 린 제조 원칙의 핵심 요소입니다.
2/ 가치 흐름 매핑: 작업 흐름 시각화
두 번째 린 원칙인 "가치 흐름 매핑"은 조직이 프로세스에서 낭비를 식별하고 제거하는 데 중요한 역할을 합니다.
가치 흐름 매핑에는 원자재의 원산지부터 제공되는 최종 제품 또는 서비스에 이르기까지 전체 프로세스에 대한 포괄적인 시각적 표현이 수반됩니다. 이 시각화는 프로세스에 관련된 활동의 순서를 이해하는 데 도움이 됩니다.
가치 흐름 매핑은 제품이나 서비스에 가치를 부여하는 활동과 그렇지 않은 활동을 구분하는 데 중요한 도구입니다. "무다(muda)"라고 불리는 비부가가치 활동은 과잉 생산, 재고 과다, 대기 시간, 불필요한 처리 등 다양한 형태의 낭비를 포함할 수 있습니다.
이러한 낭비 원인을 식별하고 제거함으로써 조직은 프로세스를 간소화하고 리드 타임을 단축하며 전반적인 운영 효율성을 향상시킬 수 있습니다.
다음은 가치 흐름 매핑의 예입니다. 이를 더 잘 이해하는 데 도움이 됩니다.
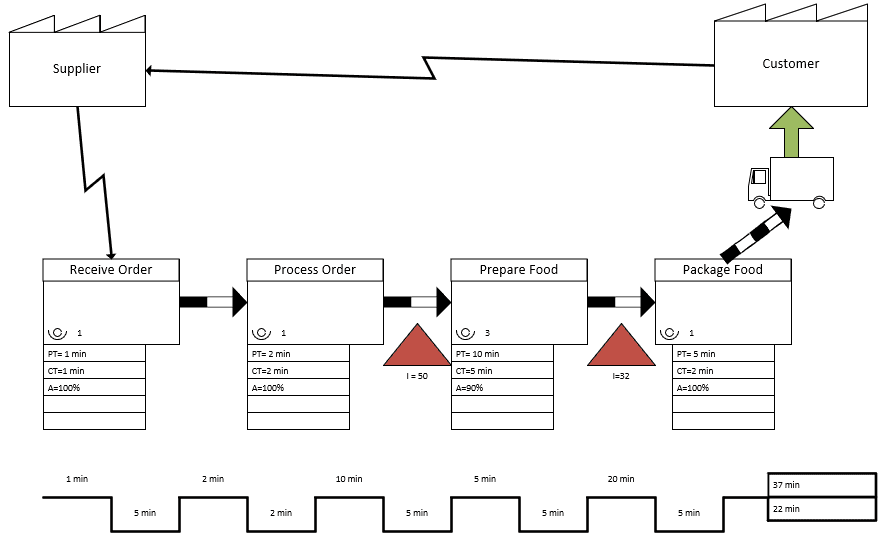
3/ 흐름: 원활한 진행 보장
"Flow"는 조직 내에서 원활하고 지속적인 업무 흐름을 창출하기 위한 것입니다. Flow의 개념은 작업이 중단이나 중단 없이 한 단계에서 다음 단계로 이동하여 궁극적으로 효율성을 높여야 함을 강조합니다.
조직의 관점에서 Lean은 업무와 활동이 방해나 지연 없이 진행되는 작업 환경을 구축하도록 권장합니다.
"흐름"을 달성하는 예로 제조 조립 라인을 생각해 보십시오. 각 스테이션은 특정 작업을 수행하며 제품은 중단 없이 한 스테이션에서 다른 스테이션으로 원활하게 이동합니다. 이는 린(Lean)의 흐름(Flow) 개념을 보여줍니다.
4/ 풀 시스템(Pull System): 수요에 대응
풀 시스템(Pull System)은 고객 주문에 응답하여 서비스를 생산하거나 제공하는 것입니다. 풀 시스템을 채택하는 조직은 미래 수요를 가정하여 품목을 제조하지 않습니다. 대신에 접수된 실제 주문에 응답합니다. 이 관행은 다음 중 하나인 과잉 생산을 최소화합니다. 일곱 가지 주요 형태의 폐기물 린 제조에서.
- 풀 시스템의 예로는 슈퍼마켓이 있습니다. 고객은 선반에서 필요한 제품을 꺼내고, 슈퍼마켓은 필요에 따라 선반에 재입고합니다. 이 시스템은 항상 고객 수요를 충족할 만큼 충분한 재고를 확보하면서도 과잉 생산이 발생하지 않도록 보장합니다.
- 풀 시스템의 또 다른 예는 자동차 판매점입니다. 고객은 관심 있는 자동차를 주차장에서 꺼내 시승을 위해 가져갑니다. 대리점은 고객 요구를 충족하기 위해 필요한 경우에만 제조업체로부터 새 자동차를 주문합니다.
5/ 지속적인 개선(카이젠)
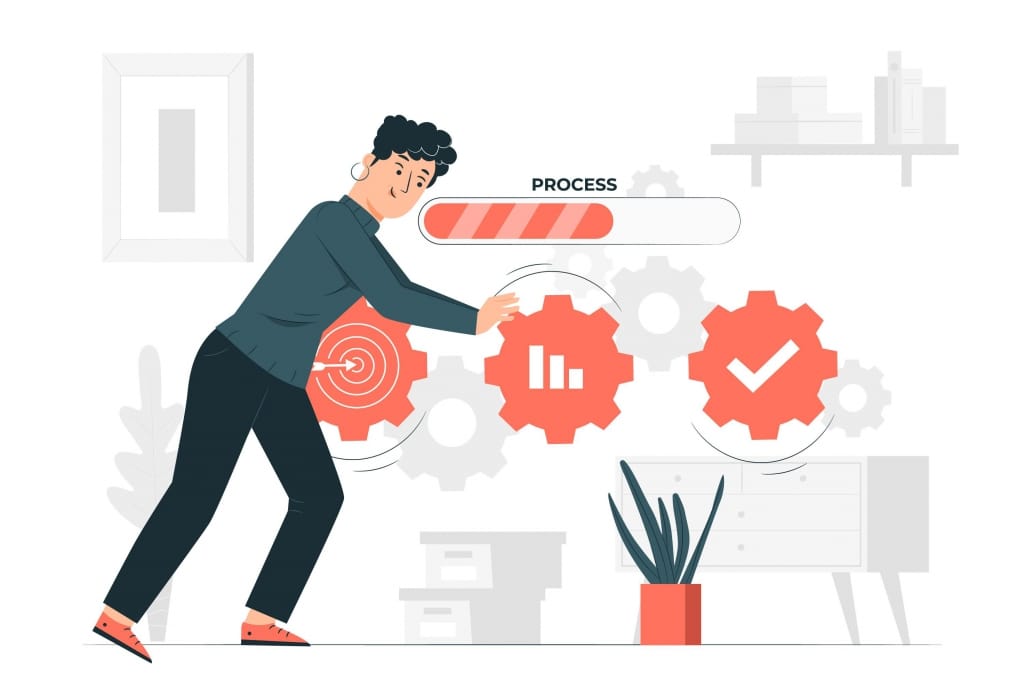
다섯 번째이자 마지막 린 원칙은 "카이젠" 또는 "지속적인 개선"으로 알려져 있습니다. 카이젠 지속적인 개선 프로세스. 지속적인 개선 문화를 조성하는 것입니다.
급진적이거나 급격한 변화를 만들기보다는 시간이 지남에 따라 작고 일관된 개선을 이루는 것이 포함됩니다. 이러한 작은 개선 사항이 합쳐져 프로세스, 품질 및 전반적인 효율성이 크게 향상됩니다.
Kaizen의 중요한 측면 중 하나는 포괄적인 특성입니다. 이는 조직의 모든 수준에서 참여를 장려하여 직원들이 자신의 아이디어, 관찰 및 통찰력을 제공할 수 있도록 합니다. 이러한 접근 방식은 문제 해결 능력을 향상시킬 뿐만 아니라 직원의 사기와 참여도도 높여줍니다.
Kaizen은 조직이 더 나은, 더 효율적이고 더 효과적으로 되기 위해 지속적으로 동기를 부여받도록 보장합니다. 이는 지속적인 개선에 대한 약속이며 린 문화의 기본 측면입니다.
최종 생각
린 제조의 5가지 원칙(가치, 가치 흐름 매핑, 흐름, 풀 시스템, 지속적 개선(카이젠))은 조직이 운영상의 우수성을 달성하기 위한 강력한 프레임워크를 제공합니다.
린 제조의 L5 원칙을 수용하는 조직은 효율성을 향상시킬 뿐만 아니라 낭비를 줄이고 제품과 서비스의 품질을 향상시킵니다.
린 제조 원칙에 대한 FAQ
린 제조의 5가지 원칙은 무엇입니까?
린 제조의 5가지 원칙은 가치, 가치 흐름 매핑, 흐름, 풀 시스템, 지속적 개선(카이젠)입니다.
5~7가지 린 원칙이 있나요?
다양한 해석이 있지만 가장 널리 알려진 린 원칙은 위에서 언급한 5가지 원칙입니다.
린 생산의 10가지 규칙은 무엇입니까?
린 생산의 10가지 규칙은 일반적으로 린 제조의 표준이 아닙니다. 린 원칙은 일반적으로 앞서 언급한 5가지 핵심 원칙을 기반으로 합니다. 일부 자료에는 "규칙"이 명시되어 있지만, 보편적으로 합의된 것은 아닙니다.