想像一下這樣一種生產方式:不浪費任何資源,每一步都讓產品更上一層樓,所有資源都能合理利用。這就是精實生產的精髓。如果你曾經好奇過一些公司是如何做到以更少的資源實現更多生產的,那麼你即將發現其中的秘密。在這篇文章中,我們將探索 精實製造的5個核心原則,帶您踏上幫助世界各地許多企業的道路。
目錄
什麼是精益製造?
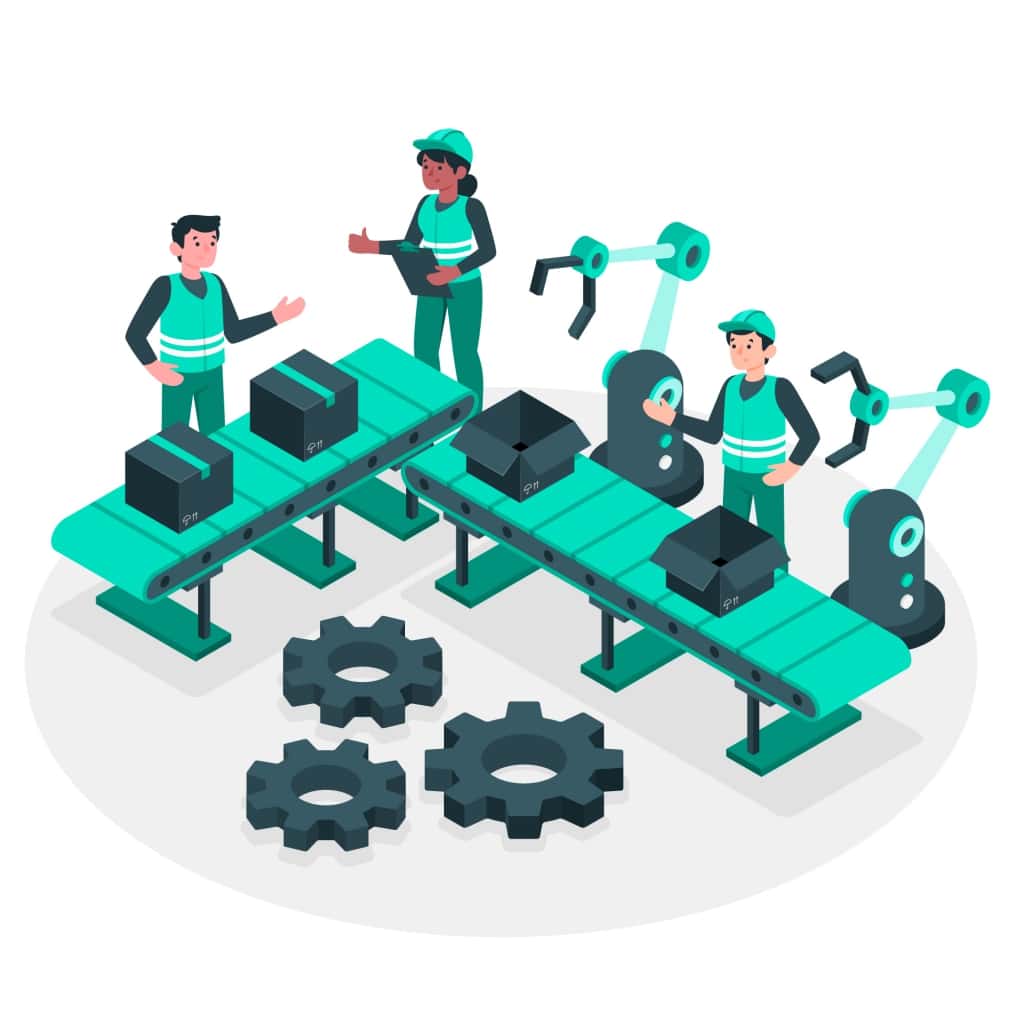
精益製造是一種系統化的生產方法,旨在減少浪費、提高效率並為客戶提供價值。 這種方法起源於 豐田生產系統 (TPS) 現在已被全球各行業和企業採用。
精益製造的主要目標是透過識別和消除任何不直接影響最終產品或服務的不必要活動、材料或資源來簡化生產流程。這有助於精簡流程並提高效率。
精實製造的好處
精益製造為旨在改善營運的公司提供了多種好處。 以下是五個主要優勢:
- 節約成本:精益製造識別並消除流程中的浪費,從而降低營運成本。 這包括降低庫存成本、減少能源消耗和減少返工,最終增加公司利潤。
- 提高效率: 透過簡化流程、消除瓶頸和優化工作流程,精實製造提高了營運效率。 這意味著企業可以用相同或更少的資源生產更多的產品,從而從投資中獲得最大收益。
- 改進的質量: 精益製造專注於識別和解決缺陷的根本原因,從而提高產品品質。 這意味著更少的錯誤、更少的返工和更高的客戶滿意度。
- 交貨更快: 精實實踐可以縮短交貨時間並更快地回應客戶需求。 按時生產和交付產品的能力可以幫助公司獲得競爭優勢並滿足客戶的期望。
- 提高員工敬業度: 精實原則鼓勵員工參與、解決問題和授權。 敬業的員工會更有動力,從而創造更積極的工作環境並持續改進。
精實製造的 5 原則
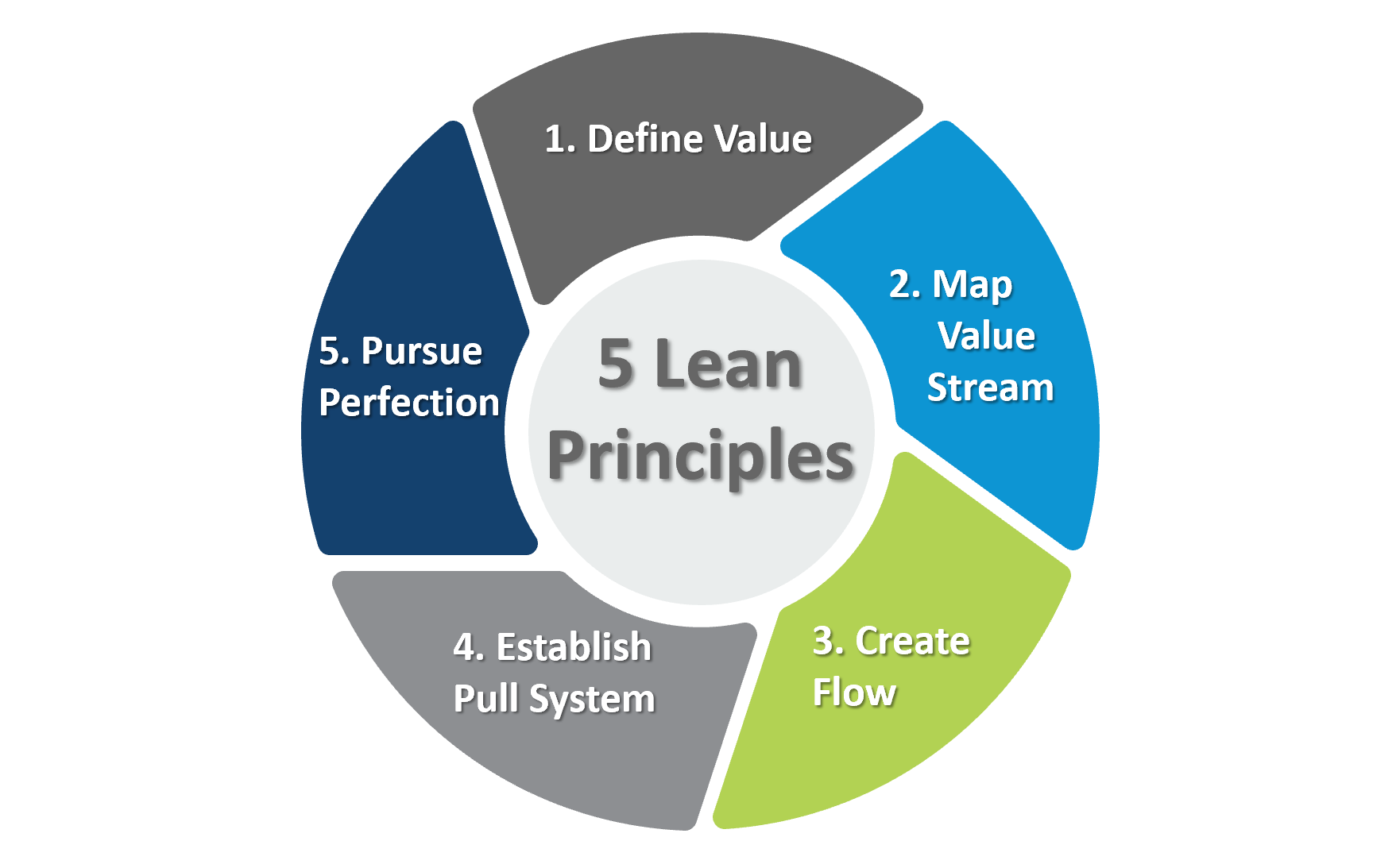
精實製造的5大原則是什麼? 精實製造的五個關鍵原則是:
1/ 價值:提供對客戶重要的東西
精實製造的首要原則是理解並交付「價值」。這理念的核心在於清楚辨識客戶在產品或服務中真正看重的是什麼。精實的價值觀以客戶為中心,旨在識別客戶願意為之付費的特定功能、品質或屬性。任何無法提供這些價值元素的產品都被視為浪費。
實現「價值」需要將企業活動與客戶的期望和需求緊密結合。透過了解客戶的真正需求,組織可以將其資源和精力用於提供真正能夠增值的產品,同時最大限度地減少或消除那些不增值的環節。這種方法可以確保資源得到有效配置,而這正是精實製造原則的關鍵。
2/ 價值流程圖:視覺化工作流程
第二個精實原則「價值流圖」在幫助組織識別和消除流程中的浪費方面發揮著至關重要的作用。
價值流圖需要創建整個過程的全面視覺表示,從原材料的來源到提供的最終產品或服務。 這種視覺化有助於理解流程中涉及的活動順序。
價值流圖是區分對產品或服務增值和不增值活動的重要工具。不加值活動通常被稱為“浪費”,包括各種形式的浪費,例如生產過剩、庫存過剩、等待時間和不必要的加工。
透過識別並消除這些浪費源,組織可以簡化流程、縮短交付週期並提高整體營運效率。
以下是價值流圖的範例,可以幫助您更好地理解它:
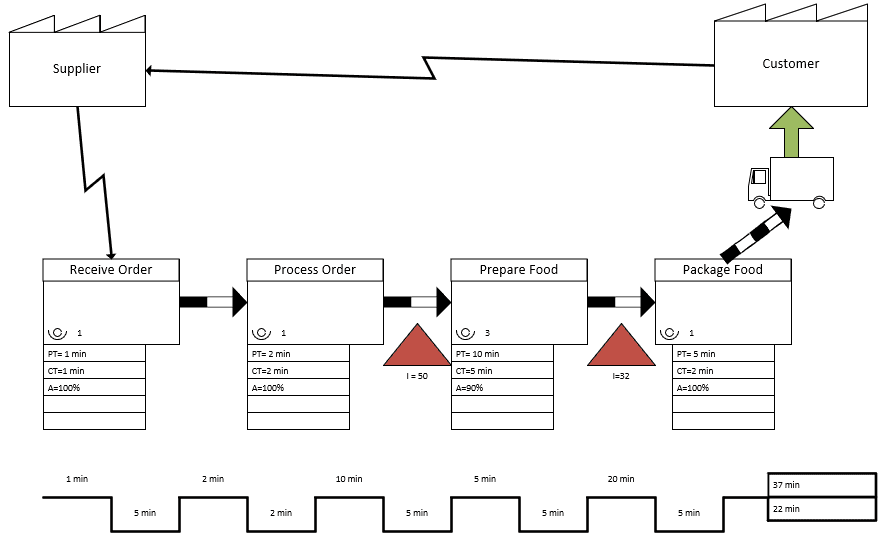
3/ 流程:確保無縫進展
「流程」旨在組織內創造平穩、持續的工作流程。 心流的概念強調工作必須從一個階段轉移到下一個階段而不會中斷或中斷,最終提高效率。
從組織的角度來看,精實鼓勵建立一個任務和活動順利進行的工作環境。
以製造裝配線為例,實現「流程」。 每個工作站執行特定的任務,產品從一個工作站無縫轉移到另一個工作站,不會中斷。 這說明了精益流程的概念。
4/ 拉動系統:回應需求
拉動系統是根據客戶訂單生產或提供服務。 採用拉動系統的組織不會根據未來需求的假設來製造產品。 相反,他們會對收到的實際訂單做出回應。 這種做法最大限度地減少了生產過剩,其中之一 七種主要廢棄物形式 在精益製造中。
- 拉式系統的例子是超市。 顧客從貨架上取下自己需要的產品,超市則依需求重新上架。 該系統確保始終有足夠的庫存來滿足客戶需求,但也不會出現生產過剩。
- 拉式系統的另一個例子是汽車經銷商。 顧客將他們感興趣的汽車從停車場拉出來並進行試駕。 經銷商僅根據需要向製造商訂購新車,以滿足客戶的需求。
5/持續改善(改善)
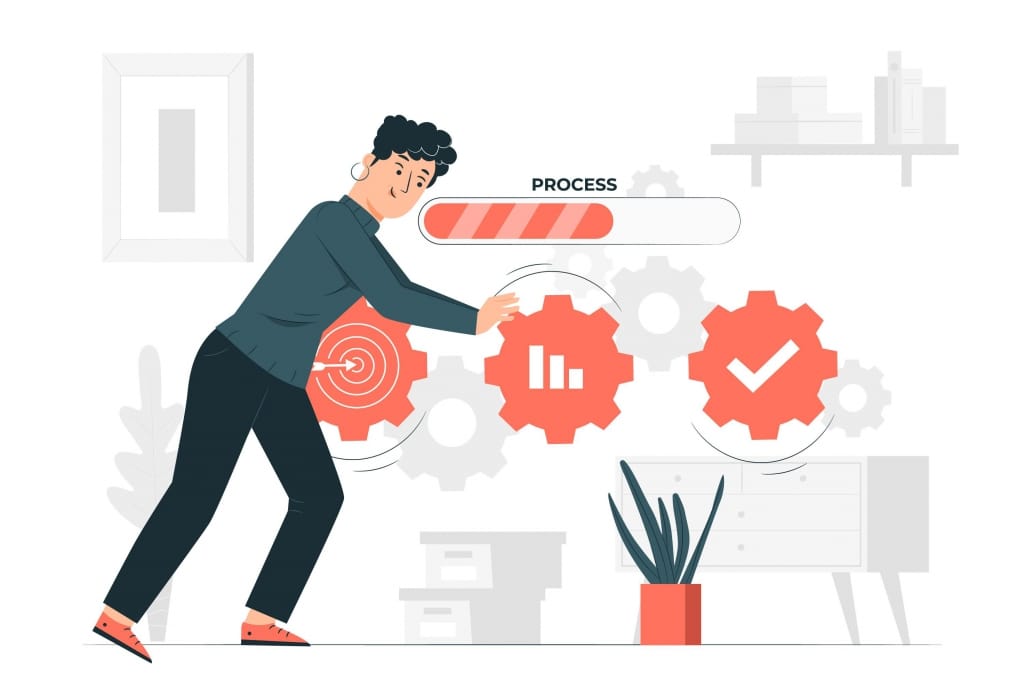
第五個也是最後一個精實原則是“持續改善”,也稱為“Kaizen”或 Kaizen 持續改善流程。 這是關於培養持續改進的文化。
它涉及隨著時間的推移進行小的、持續的改進,而不是進行根本性或劇烈的改變。 這些微小的改進加起來,會導致流程、品質和整體效率的顯著進步。
Kaizen 的重要方面之一是其綜合性。 它鼓勵組織各層面的參與,讓員工貢獻他們的想法、觀察和見解。 這種方法不僅提高了解決問題的能力,也提高了員工的士氣和參與度。
Kaizen 確保組織持續受到激勵,變得更好、更有效率、更有效率。 它是對持續改善的承諾,也是精實文化的一個基本面向。
最後的思考
精實製造的 5 項原則:價值、價值流圖、流程、拉動系統和持續改善(Kaizen)-為組織提供實現卓越營運的強大框架。
採用 L5 精益製造原則的組織不僅可以提高效率,還可以減少浪費並提高產品和服務的品質。
有關精實製造原則的常見問題解答
精實製造的5大原則是什麼?
精實製造的 5 項原則是價值、價值流圖、流程、拉動系統和持續改善(Kaizen)。
有 5 或 7 個精實原則嗎?
雖然有不同的解釋,但最廣泛認可的精實原則是上面提到的 5 個。
精實生產的10條規則是什麼?
精實生產的十條規則通常並非精實製造的標準。精實原則通常是基於前面提到的五個核心原則。有些資料來源可能會列出“規則”,但這些規則並非普遍認可的。